I'm playing around with workplace illumination and have developed a 20 V "“> 38 V PWM'able constant current source to drive my power LEDs (max power about 64W). So far, so good. However, I've nearly thermally killed one LED by fixing it on a significantly undersized heat sink ("luckily", the wire contacts unsoldered themselves just in time, stopping the process).
Now, I'm considering cooling options. Wanting to avoid active cooling (i.e. the humming of a fan), I was considering the "lazy" way out (dimension far from final, I don't have a heatsink candidate yet):
I'd like to mount the 19 x 19 mm LED directly onto an aluminum bar or profile. Now, I'm already playing around with thermal simulation software, but that seems over the top (and so far, it mostly crashes, plus I have a lot of theory to catch up on).
One 60W LED is a thermal challenge because the heat source is small and very powerful. Therefore, you will need thick metal to spread the heat laterally into a large enough heatsink.
This is similar to a desktop PC cpu: small surface area, lots of power. Many desktop PC heat sinks use heat pipes to solve the heat spreading problem. A fanless PC heatsink should work.
However, this doesn't solve the other problem, which is that one 60W LED is a very bright point source, and it is not ideal for workplace illumination. It will be blindingly bright and will cast harsh shadows.
So:
Is there a well-known analytic model for heat distribution when attaching a constant-power heat source to a piece of metal?
if not, is there a go-to simulation software? So far, I'm playing with Elmer.
Is simulation the way to go here, at all, or is passive cooling damned for 60W LEDs?
Can I solve both problems by using LED strips like this TLHB4201, datasheet: http://www.kynix.com/uploadfiles/pdf9675/TLHB4201.pdf
Junction-Case Thermal Resistance 0.8 K/W
19x19 mm
max rated power 64.2 W
continuous power I'm planning to use: 36.6 V · 0.72 A = 26.352 W
Now, I'm considering cooling options. Wanting to avoid active cooling (i.e. the humming of a fan), I was considering the "lazy" way out (dimension far from final, I don't have a heatsink candidate yet):
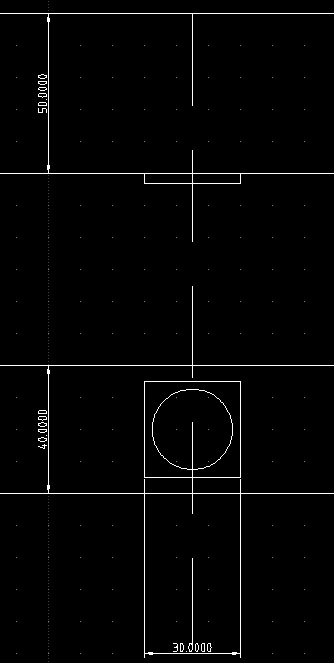
I'd like to mount the 19 x 19 mm LED directly onto an aluminum bar or profile. Now, I'm already playing around with thermal simulation software, but that seems over the top (and so far, it mostly crashes, plus I have a lot of theory to catch up on).
One 60W LED is a thermal challenge because the heat source is small and very powerful. Therefore, you will need thick metal to spread the heat laterally into a large enough heatsink.
This is similar to a desktop PC cpu: small surface area, lots of power. Many desktop PC heat sinks use heat pipes to solve the heat spreading problem. A fanless PC heatsink should work.
However, this doesn't solve the other problem, which is that one 60W LED is a very bright point source, and it is not ideal for workplace illumination. It will be blindingly bright and will cast harsh shadows.
So:
Is there a well-known analytic model for heat distribution when attaching a constant-power heat source to a piece of metal?
if not, is there a go-to simulation software? So far, I'm playing with Elmer.
Is simulation the way to go here, at all, or is passive cooling damned for 60W LEDs?
Can I solve both problems by using LED strips like this TLHB4201, datasheet: http://www.kynix.com/uploadfiles/pdf9675/TLHB4201.pdf
Junction-Case Thermal Resistance 0.8 K/W
19x19 mm
max rated power 64.2 W
continuous power I'm planning to use: 36.6 V · 0.72 A = 26.352 W