Hi guys. Just thought it's about time to share what we've been working on for quite some time. As you all know, we are pretty addicted to this hobby and have been looking to expand for quite some time. Some of you have seen this project in the works...
What it is:
A dedicated fish room/structure build. After months of research and number crunching, we decided to build a permanent, permitted and inspected, structure to house this new upcoming system. Building a green house was tempting, in order to use sunlight to grow coral, but after having done the calculations of trying to heat in the winter and cool in the summer, I don't think it would have been as feasible. In addition, if we ever decided to scrap the entire idea, we would guess the resale value of a huge green house would have been really crappy, whereas this building will undoubtedly add considerable value.
We're at the point now where we're starting to finalize the construction portion of this, and if we're going to add anything else, or modify anything, before we close the walls up, now would be the time. For those of you that have dedicated fish rooms, we'd love to hear any input about your experiences. Specifically electrical, ventilation, heating/cooling. Any other cool stuff you guys have, or regret not doing, please let us know. Open to any criticism!
Some general specs:
Building foundation consists of 27" deep footings. Foundation poured in two stages (footings, and then the 10" - 12" thick slab). Yes.. it's that thick! The footings were constructed with a curb/stem wall type design, so that none of the wood framing ever touches the floor (we realistically expect many, many floods will happen). Structure is 30'x20' with 10' ceilings framed with 2x4 walls, 2x8 ceiling joists. Two large double pane argon filled windows (6'x6' and 8'x6). One 8' three layer insulated roll up garage door, 2" thick. One entry door. Roof is regular asphalt shingles with ridge vents and finished tongue and groove soffits.
Electrical:
Service is being upgraded to 400 amps for our entire home. This building will have a dedicated 200 amp panel, which should hopefully be just enough for what we have planned. A 20,000 watt standby generator will be installed, tied to natural gas, which will hopefully help during power outages. It has a 400 amp automatic transfer switch and is fully automated. There will be many, many, separate circuits ran. I'm guessing there will be a dedicated 20 amp circuit for lighting, per tank, which will be bypassed, and not powered by the generator, at least not automatically (in an effort to avoid overloading the generator). As of right now, we're told that SCE needs to upgrade their infrastructure to support the added draw.. For this reason, our service won't be switched over for another 4-5 months until their transformer and secondaries are all replaced, as well as the pole they are on. Solar is something that will definitely be added later down the road.
Ventilation/heating/cooling:
We plan to use multiple bathroom style exhaust fans, on timers, to exhaust some of the humidity. I don't have much experience with humidistats and would love input. There will also be a 30,000 BTU separated combustion gas heater to help during the cooler winter months (it gets into the 20's here). For cooling, we plan to use a LG 3 ton ductless, mini-split AC system with 3x 9000 BTU units (it gets over 100+ in the summer). I really hope they hold up to the saltwater environment.. Any one use these?? We purchased the system a few years ago but never installed it, due to an out dated electrical system, so now is our chance to put it to use in this building instead. Heating for the tanks will be via a recirculating gas hot water heater system. We plan to use no electrical heaters whatsoever.
Walls:
We plan to drywall, then install FRP over all the walls. The walls/ceiling will all be insulated with standard batts. I want the entire interior to be water proof, with water proof outlet boxes.
Tank racks/stands:
There will be 4 rows of industrial type warehouse racks, all welded, braced, and connected at the top for stability. This will give us 5 aisles to work with, allowing access to most of the tanks from both sides. We plan to have three levels of tanks to maximize our small amount of square footage we have to work with.
Tanks (all 12" deep, glass):
3x 7'x'2'
6x 8'x2.5'
3x 8x4'
There will later be a QT system, as well as other smaller tanks for anemone propagation, etc. Sumps to be determined..
Lighting:
We plan to use primarily metal halide and T5 lighting. Only a limited number of LED fixtures. We plan to have the lighting on for the different levels in 8 hour blocks. That way, there will be lights on, 24 hours a day and should help keep the temperature/ph more stable during the cooler winter months. Based on some quick numbers, when all the lights are on over each tank, there will be close to a 20,000 watt draw on the electrical system.. yikes.
Flow:
We plan to use primarily Vortech MP pumps. Probably 5x mp40's on each of the smaller tanks, and larger pumps on the larger tanks. The return pumps will probably be Reeflo hammerheads, with some type of flow meter, connected to a back up return pump. We got the idea after reading about Bill Wann's 20,000 gallon set up. We need to do more research, but are interested in running a cati/ani type of water filtration system, tied to a Genesis auto water change system. The building will have full plumbing with multiple stainless steel sinks, as well as one 9' long stainless drain tray. One floor drain in the center as well, even though the slab is sloped towards the roll up door.
Control:
We hope to use the APEX to control most of this system. I have no clue how, or if it is even possible, to incorporate multiple temperature probes, and ph probes, etc, for redundancy. One thing is for certain, and I have past experience with this.. There is no way in hell I'm trusting this entire system to a $30 apex temperature probe. If anyone has any experience with using multiple probes for redundancy, I would love to hear from you.
Display tank:
We plan to re-use the tank we got from KingGeorge as our glass display tank, right by the roll up door. The tank is 10' x 3' x 2.5' tall. This tank will be its own separate system.
That's pretty much the jist of it at this point. At this stage, we are waiting for the natural gas meter to be upsized, and the install of the electrical panels/stand by generator/gas heater to be completed.
Below are some pics of the progress from the time we started back in late 2013.. We tried to do the majority of the work ourselves. Most of the construction was completed by April, 2014, and then we took a long break to build up some funds and most importantly.. rest. In that span, we have accumulated quite a bit of extra equipment, which we realized we probably won't be re-using. So.. we purchased a new 20' ocean shipping container as temporary storage.
We're all ears at this point. We hope to have at least some tanks full of water by the middle of this year, and it will definitely take quite some time to grow into the rest of the system..
Thanks for reading and give us some feedback..
What it is:
A dedicated fish room/structure build. After months of research and number crunching, we decided to build a permanent, permitted and inspected, structure to house this new upcoming system. Building a green house was tempting, in order to use sunlight to grow coral, but after having done the calculations of trying to heat in the winter and cool in the summer, I don't think it would have been as feasible. In addition, if we ever decided to scrap the entire idea, we would guess the resale value of a huge green house would have been really crappy, whereas this building will undoubtedly add considerable value.
We're at the point now where we're starting to finalize the construction portion of this, and if we're going to add anything else, or modify anything, before we close the walls up, now would be the time. For those of you that have dedicated fish rooms, we'd love to hear any input about your experiences. Specifically electrical, ventilation, heating/cooling. Any other cool stuff you guys have, or regret not doing, please let us know. Open to any criticism!
Some general specs:
Building foundation consists of 27" deep footings. Foundation poured in two stages (footings, and then the 10" - 12" thick slab). Yes.. it's that thick! The footings were constructed with a curb/stem wall type design, so that none of the wood framing ever touches the floor (we realistically expect many, many floods will happen). Structure is 30'x20' with 10' ceilings framed with 2x4 walls, 2x8 ceiling joists. Two large double pane argon filled windows (6'x6' and 8'x6). One 8' three layer insulated roll up garage door, 2" thick. One entry door. Roof is regular asphalt shingles with ridge vents and finished tongue and groove soffits.
Electrical:
Service is being upgraded to 400 amps for our entire home. This building will have a dedicated 200 amp panel, which should hopefully be just enough for what we have planned. A 20,000 watt standby generator will be installed, tied to natural gas, which will hopefully help during power outages. It has a 400 amp automatic transfer switch and is fully automated. There will be many, many, separate circuits ran. I'm guessing there will be a dedicated 20 amp circuit for lighting, per tank, which will be bypassed, and not powered by the generator, at least not automatically (in an effort to avoid overloading the generator). As of right now, we're told that SCE needs to upgrade their infrastructure to support the added draw.. For this reason, our service won't be switched over for another 4-5 months until their transformer and secondaries are all replaced, as well as the pole they are on. Solar is something that will definitely be added later down the road.
Ventilation/heating/cooling:
We plan to use multiple bathroom style exhaust fans, on timers, to exhaust some of the humidity. I don't have much experience with humidistats and would love input. There will also be a 30,000 BTU separated combustion gas heater to help during the cooler winter months (it gets into the 20's here). For cooling, we plan to use a LG 3 ton ductless, mini-split AC system with 3x 9000 BTU units (it gets over 100+ in the summer). I really hope they hold up to the saltwater environment.. Any one use these?? We purchased the system a few years ago but never installed it, due to an out dated electrical system, so now is our chance to put it to use in this building instead. Heating for the tanks will be via a recirculating gas hot water heater system. We plan to use no electrical heaters whatsoever.
Walls:
We plan to drywall, then install FRP over all the walls. The walls/ceiling will all be insulated with standard batts. I want the entire interior to be water proof, with water proof outlet boxes.
Tank racks/stands:
There will be 4 rows of industrial type warehouse racks, all welded, braced, and connected at the top for stability. This will give us 5 aisles to work with, allowing access to most of the tanks from both sides. We plan to have three levels of tanks to maximize our small amount of square footage we have to work with.
Tanks (all 12" deep, glass):
3x 7'x'2'
6x 8'x2.5'
3x 8x4'
There will later be a QT system, as well as other smaller tanks for anemone propagation, etc. Sumps to be determined..
Lighting:
We plan to use primarily metal halide and T5 lighting. Only a limited number of LED fixtures. We plan to have the lighting on for the different levels in 8 hour blocks. That way, there will be lights on, 24 hours a day and should help keep the temperature/ph more stable during the cooler winter months. Based on some quick numbers, when all the lights are on over each tank, there will be close to a 20,000 watt draw on the electrical system.. yikes.
Flow:
We plan to use primarily Vortech MP pumps. Probably 5x mp40's on each of the smaller tanks, and larger pumps on the larger tanks. The return pumps will probably be Reeflo hammerheads, with some type of flow meter, connected to a back up return pump. We got the idea after reading about Bill Wann's 20,000 gallon set up. We need to do more research, but are interested in running a cati/ani type of water filtration system, tied to a Genesis auto water change system. The building will have full plumbing with multiple stainless steel sinks, as well as one 9' long stainless drain tray. One floor drain in the center as well, even though the slab is sloped towards the roll up door.
Control:
We hope to use the APEX to control most of this system. I have no clue how, or if it is even possible, to incorporate multiple temperature probes, and ph probes, etc, for redundancy. One thing is for certain, and I have past experience with this.. There is no way in hell I'm trusting this entire system to a $30 apex temperature probe. If anyone has any experience with using multiple probes for redundancy, I would love to hear from you.
Display tank:
We plan to re-use the tank we got from KingGeorge as our glass display tank, right by the roll up door. The tank is 10' x 3' x 2.5' tall. This tank will be its own separate system.
That's pretty much the jist of it at this point. At this stage, we are waiting for the natural gas meter to be upsized, and the install of the electrical panels/stand by generator/gas heater to be completed.
Below are some pics of the progress from the time we started back in late 2013.. We tried to do the majority of the work ourselves. Most of the construction was completed by April, 2014, and then we took a long break to build up some funds and most importantly.. rest. In that span, we have accumulated quite a bit of extra equipment, which we realized we probably won't be re-using. So.. we purchased a new 20' ocean shipping container as temporary storage.
We're all ears at this point. We hope to have at least some tanks full of water by the middle of this year, and it will definitely take quite some time to grow into the rest of the system..
Thanks for reading and give us some feedback..
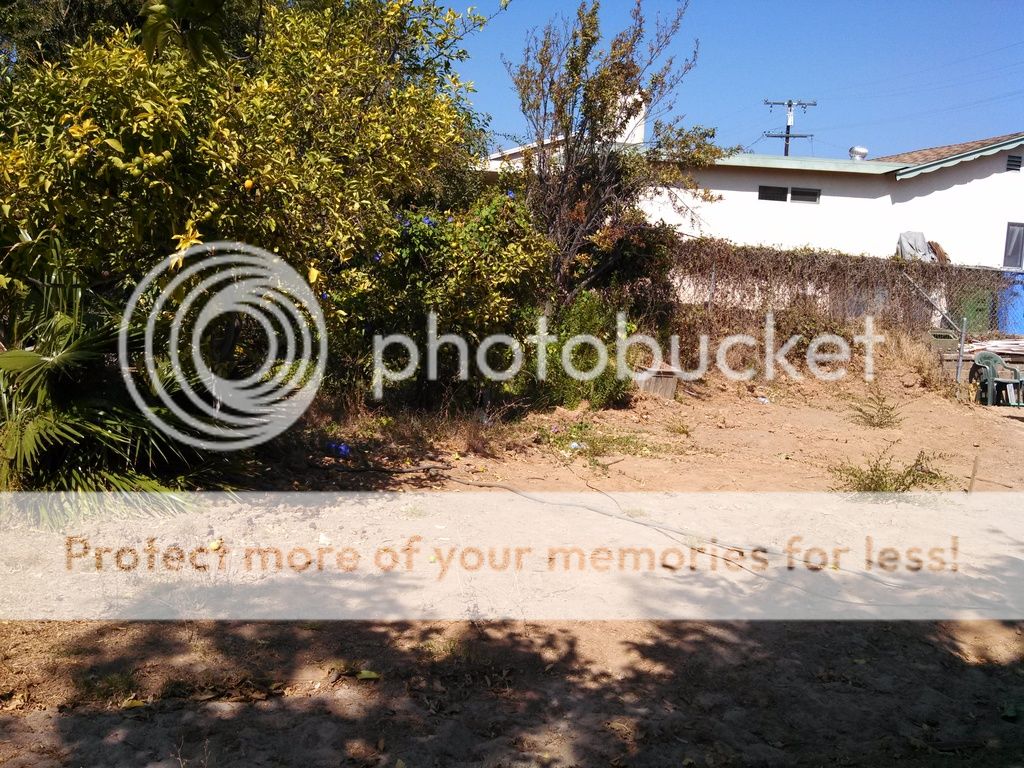
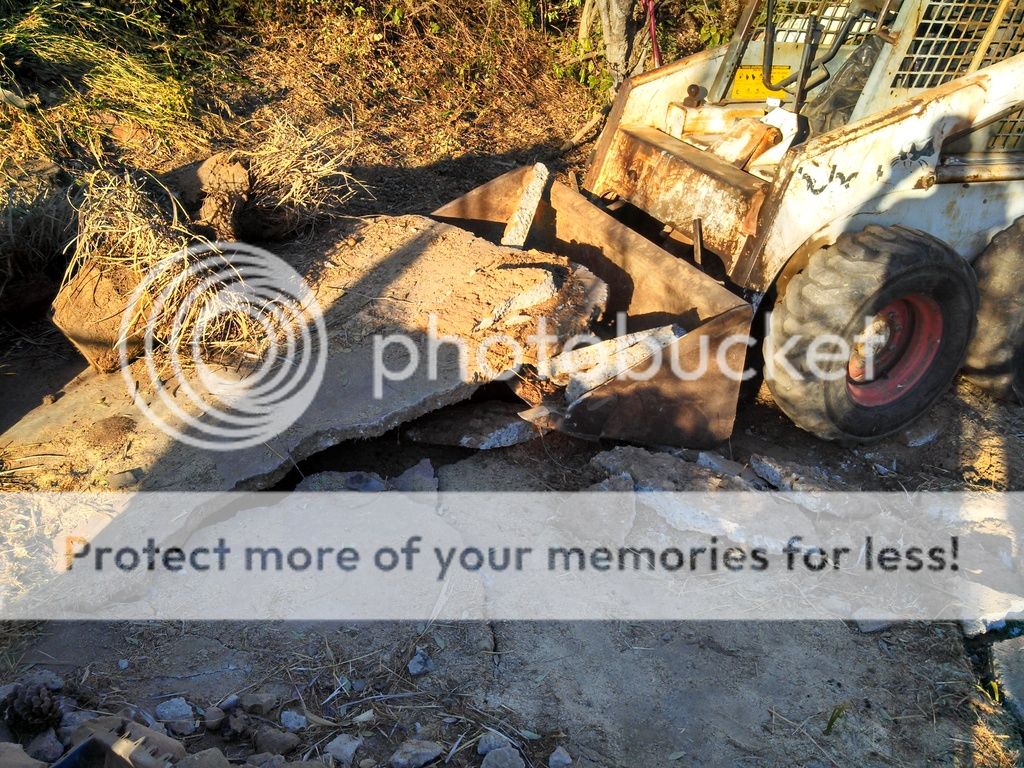
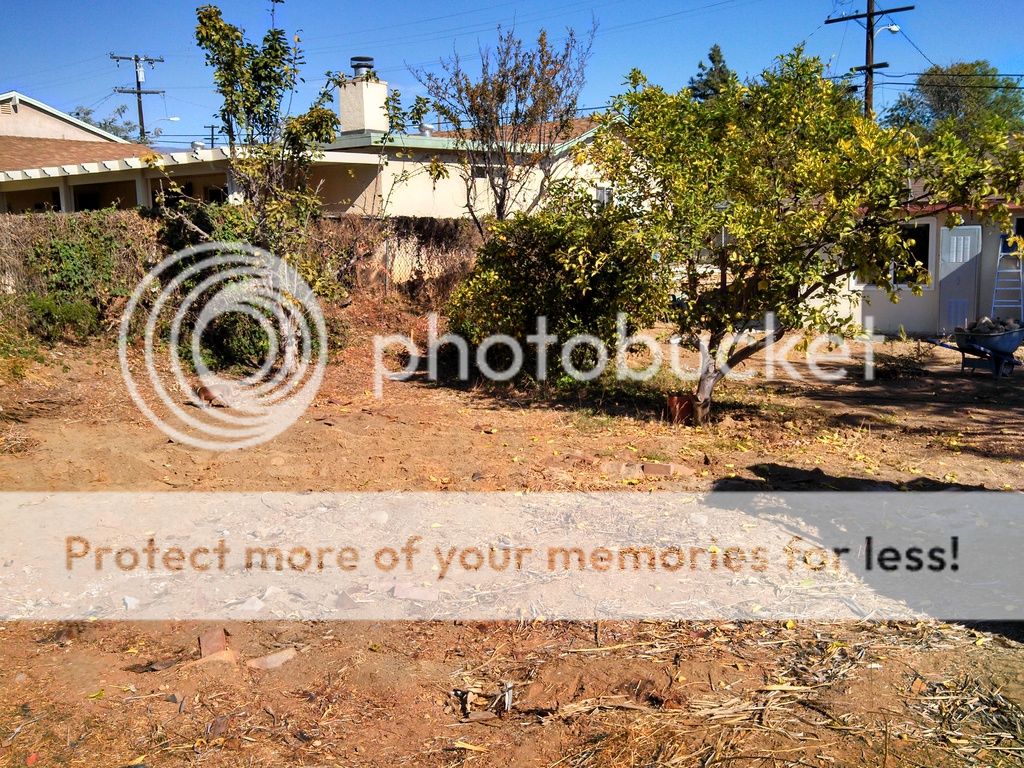
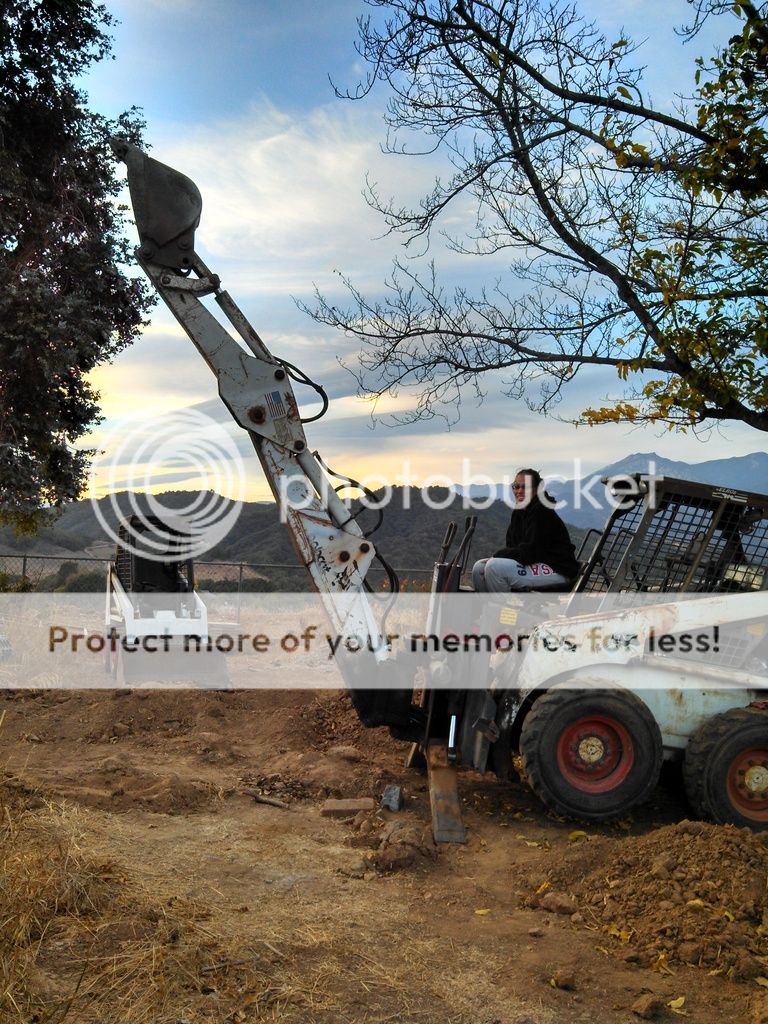
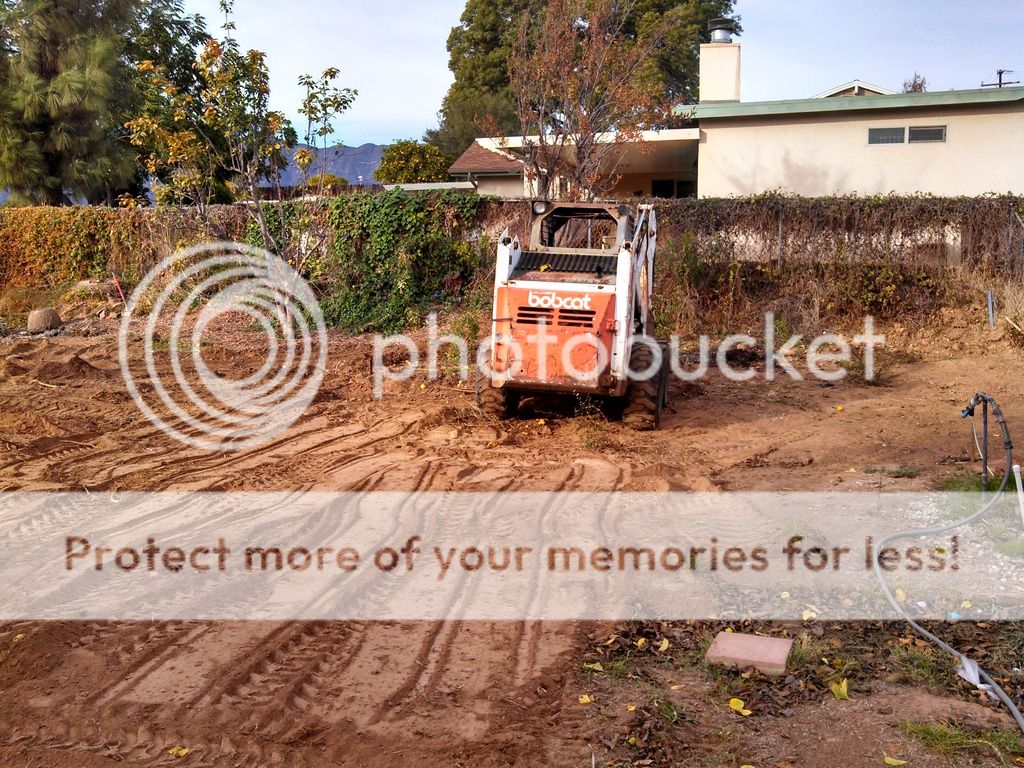
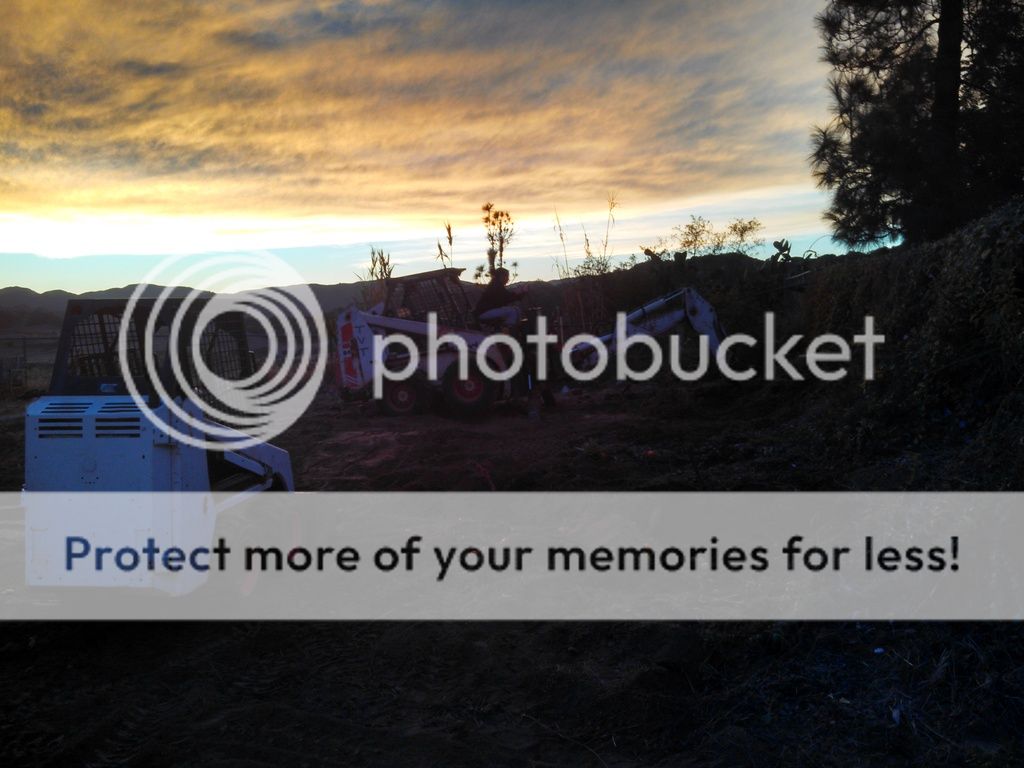
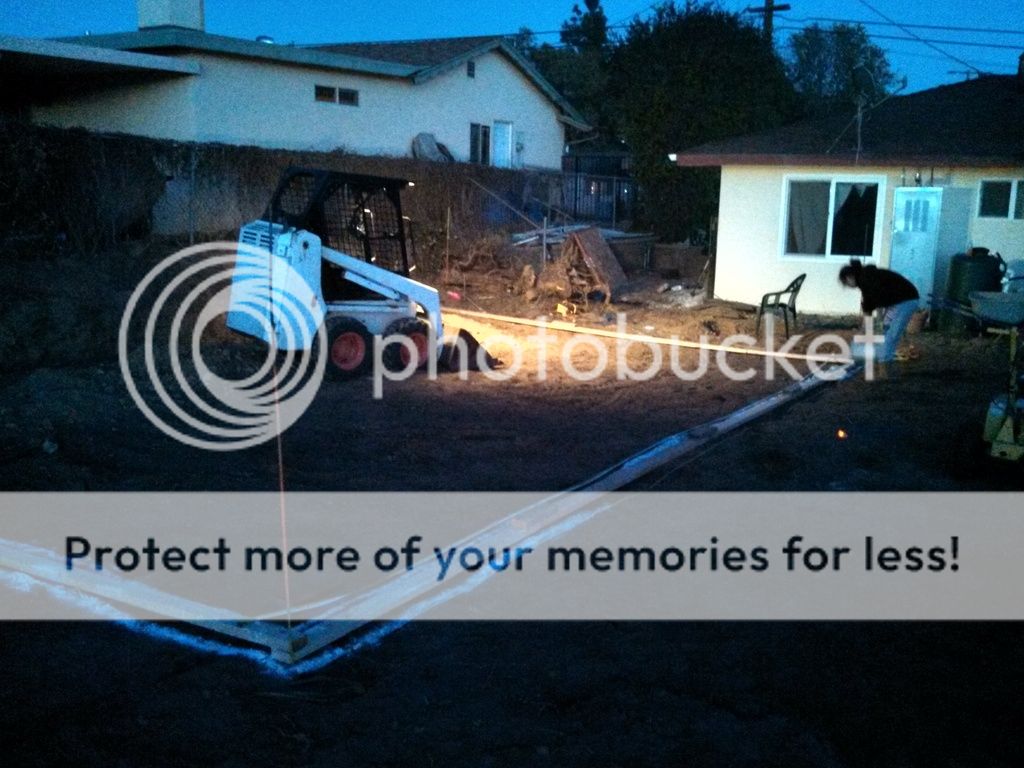
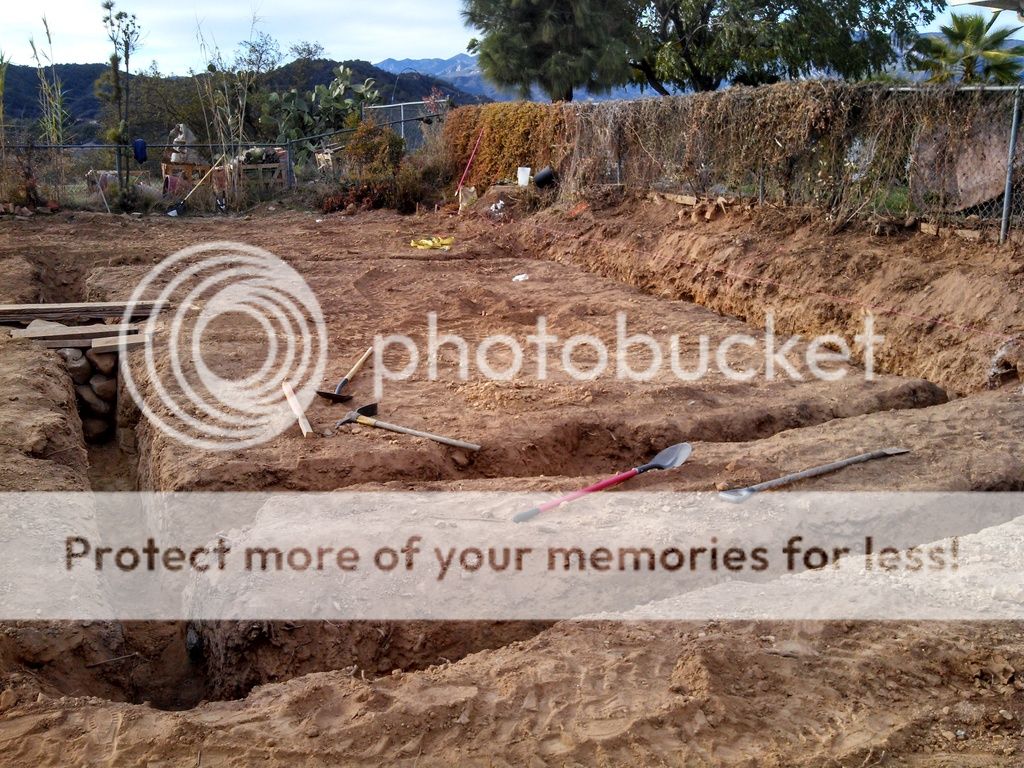
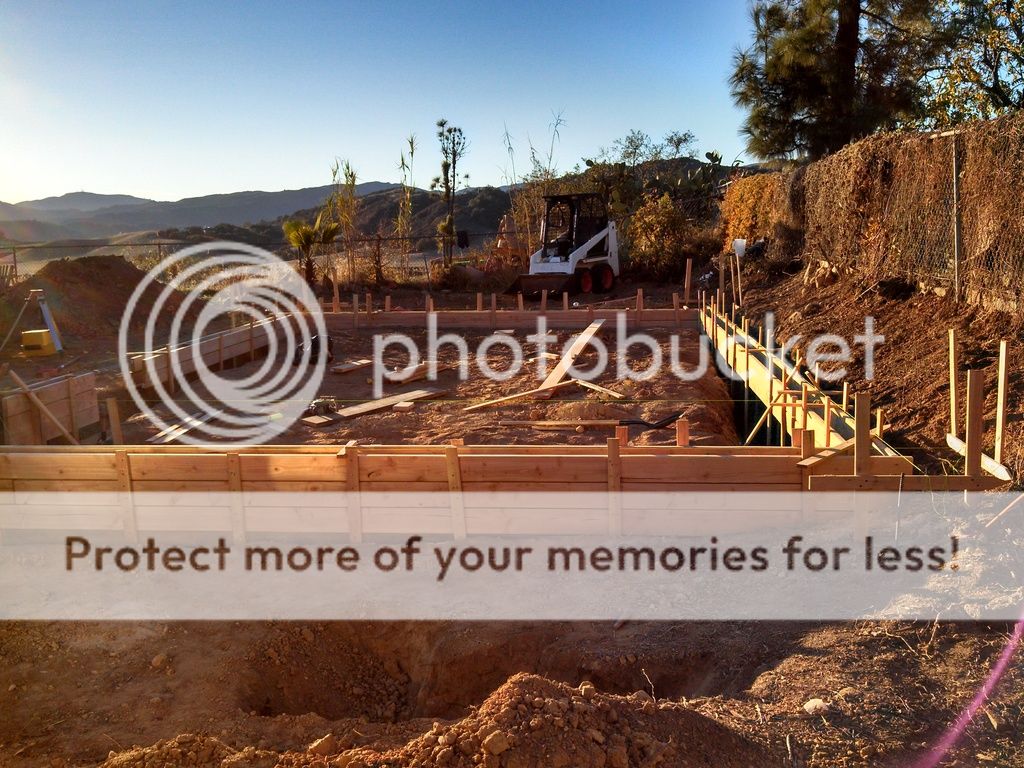
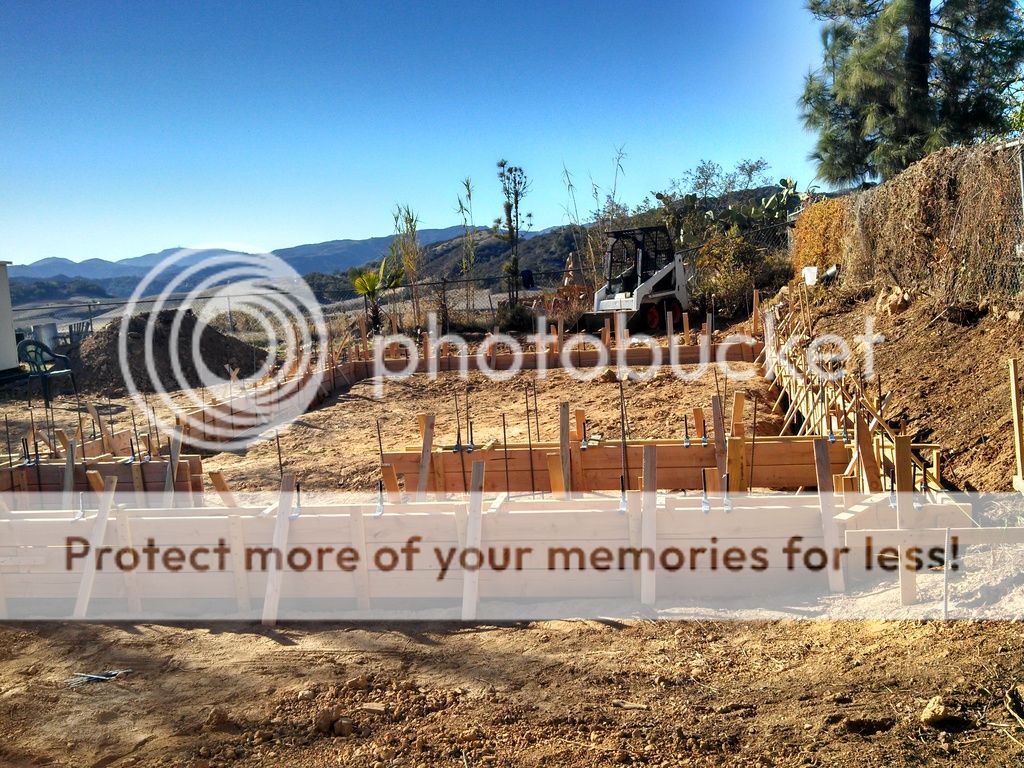