mcbaes72
-Aidan's Daddy.
What an amazing thread to find. Ive been thinking of making a steel stand for my 7x2x2.5 Im looking to have as much open space at the front for sump access (as we all are) Do any of you guys have a design that you have used for a tank of this size?
If I could re-do my stand, I'd go over-built like this:
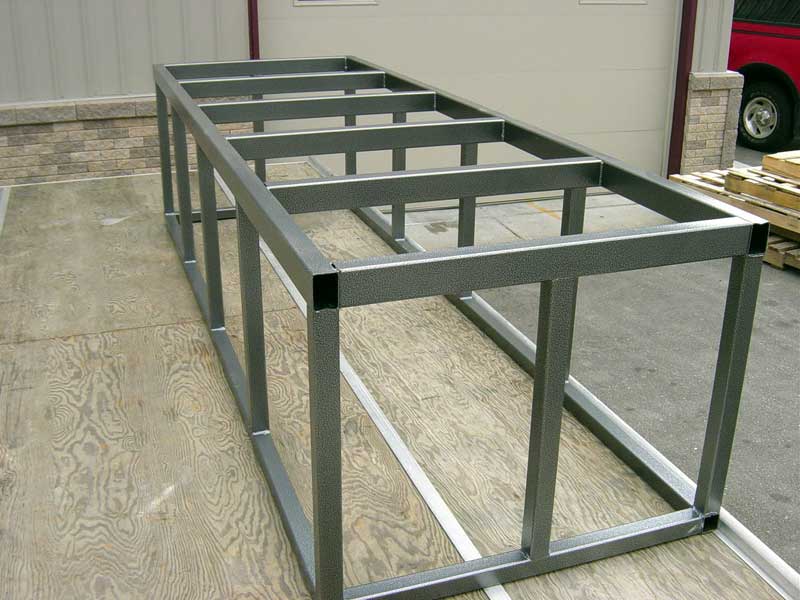
Plenty of space in the front, lots of extra support in the back.
Last edited: